10 Years of Modality Solutions: What We’ve Learned, Part 2
In our previous post, we looked at some of the ways the biopharmaceutical industry...
read Details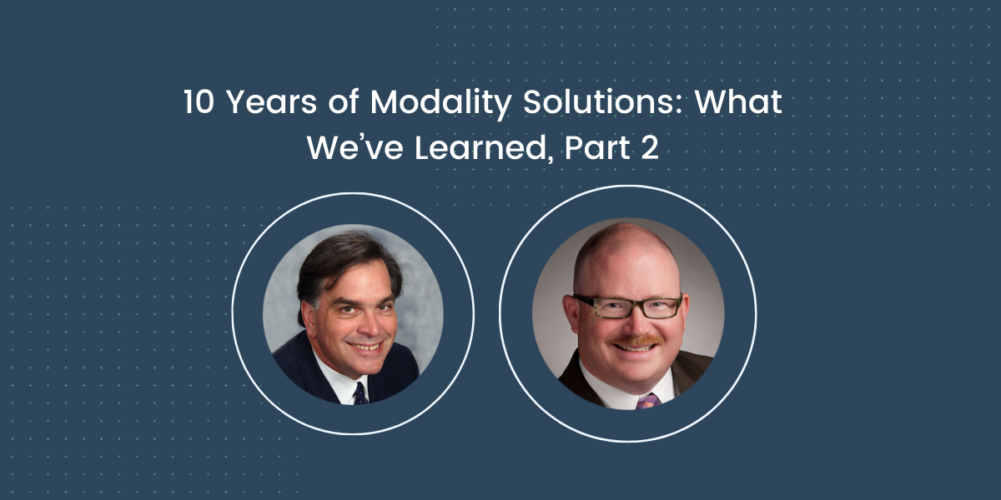
Recently, we worked on a project for an advanced CAR T-cell therapy developed by innovators without much experience navigating the cold chain. Last week, its parent company announced that “patient one” no longer requires insulin injections, showing real promise that this therapy could cure diabetes.
Optimizing and managing the cold chain to ensure safe shipment of drug product—what we call Cold Chain Engineering™—plays a huge role in success stories like these. It’s taken the biopharmaceutical industry a long time to come around to this way of thinking. But over the last ten years, we’ve contributed in efforts to make efficient, cost-effective shipment testing an industry standard.
Here’s what we’ve learned along the way.
Since we established Modality Solutions in 2011, we have seen constant reminders that what we do has an impact on hundreds of thousands of lives every day. Unfortunately, the industry hasn’t always seen it that way.
When we first started putting a team together, it was difficult to find engineering talent who saw the opportunity in this newer industry. Few people believed in the impact the cold chain could bring to our understanding of how complex molecules can hold up in transit.
Today, we’re reminded every day about how the decision we made 10 years ago has changed the path of temperature-sensitive drugs and biologics. The impact is enormous and sometimes impossible to quantify.
For example, we worked with the CDC on the Ebola epidemic. The initial effort to transport vaccine shipments to African nations saved some portion of the 13,000 people who were vaccinated in that wave. From there, subsequent waves have seen the cold chain as instrumental in getting tens of thousands of people the drugs they need, when the mortality has been as high as 60% in places like the Democratic Republic of the Congo.
It’s not just the public health initiative pushes that make a big difference. Before we started Modality Solutions, I (Gary) was on the team that commercialized one of the first biologics. When there were significant challenges in shipping it, I had access to the resources of the world’s largest biotechnology companies to reproduce logistics scenarios and determine what pieces were missing on shipping controls.
We realized, as more and more biologics were developed and tested, other companies were going to need engineering services to develop therapies on this same platform. Many wouldn’t have the multi-million dollar budget needed to develop new equipment, test processes, or use significant amounts of drug product for real-world tests.
Today, we get to put our Cold Chain Engineering™ expertise to the test with larger established pharmaceutical companies as well as smaller ones. The virtual innovators may know there is a regulatory expectation for analytical testing work post-distribution to confirm there are no drug product quality issues. But they may only know about large-scale real-world shipping tests.
Smaller companies are relieved to hear that you can do the same testing with a small amount of product (20-30 vials instead of thousands) in a similar environment and get a better answer. It can also come at a much lower cost than they thought possible.
These smaller companies are often passionately working on orphan diseases with an underserved patient population. They have an opportunity to make a gigantic impact on patients, but they may not have the funding to put every piece of the puzzle together themselves. Seeing them get positive feedback from the approval agency and get something done in 18 months that would take years to achieve with big pharma is one of the best parts of the job.
When we had access to large biotechnology testing capabilities (prior to founding Modality Solutions), it was still difficult to figure out what was going on when we ran into trouble with a molecule. It became obvious that you couldn’t solve every problem by testing separately for each of the hazards that could damage a molecule (temperature, pressure, humidity, shock, and vibration). This had to be done concurrently.
It took a few years at Modality Solutions to build the prototype of our own Advantage Transport Simulation Laboratory™, but we had other work to do. Our first and most important task was to inform the industry that there’s a better way to test drugs than shipping mass amounts of product around the world. Today, our approach is an industry standard—but it was a long road getting here.
So how do you go about asking an industry that’s slow to change to recognize the value of this approach to validation work?
It’s like sumo wrestling. You push and push and push until something budges.
We showed up everywhere we could, spending time at tradeshows and conferences to get the word out. But we made it a point to provide information at our workshops that was actually useful, rather than creating a 3-hour paid infomercial. We learned that the industry is good at separating the real deal from the sales pitch. Honesty and credibility were our sharpest tools.
We had the answers to questions you couldn’t find with real-world shipping studies. By the time our Advantage Transport Simulation Lab was calibrated and validated, we had proved it to be a better and faster route to approval.
The last ten years have been very viral for us, and referrals have carried us a long way. Now, we’ve carved out a space in the cold chain where good science and good engineering meet, using interdisciplinary engineering work to make a difference in cold chain validation of both the drug product and the logistics processes. This perseverance has been the real change element, helping to change the industry one company and one molecule at a time.
Stay tuned for part two of our look back on 10 years.
Contact Modality Solutions to learn how 10 years of Cold Chain Engineering™ expertise can change the path of your therapeutic.
In our previous post, we looked at some of the ways the biopharmaceutical industry...
read DetailsFirst published on January 5, 2016 on Cold Chain IQ – as a contributor,...
read DetailsFirst published on September 16, 2015 on Cold Chain IQ – as a contributor,...
read Details