The Negatives of Real-World Shipping Studies for the Biopharma Cold Chain
Executive Summary:
There’s a time and a place for Real-World Shipping studies, but when it comes to testing drug product robustness at the operating edge of your supply chain against concurrent transportation hazards, real-world shipping studies just won’t cut it.
Andrew Larrigan (Modality Solutions’ Transport Simulation Lab – Technical Operations Manager and engineer), has outlined key reasons why real-world shipping studies are inadequate, and details the clear solution below.
When drug product (DP) robustness is not evaluated properly through the supply chain, there is a significant risk to patient safety. It is critical for pharmaceutical and biopharma companies to test how well their drug formulation will endure worst-case environmental hazards (shock, vibration, low pressure, temperature, and humidity) they will face in their supply chain. With no downstream confirmation of DP quality after manufacturing and filling, and no visual indication of a DP quality issue, it’s vital to ensure the DP is robust to these distribution hazards (especially for temperature and physically sensitive biologics).
Real-world shipping studies are appropriate when conducting performance qualifications (PQs) of your shipping lanes. These studies investigate your thermal packaging performance with the focus on temperature control (no drug product analytical testing) to ensure that your shipping process is well-defined and operating in a state of control.
Pharma companies often turn to real-world shipping tests in hopes that they can also prove their drug product is robust to distribution hazards. However, to test drug formulations for physical and chemical stability at the operating edge of your supply chain, you must use an adequate shipping validation strategy like concurrent hazard transport simulation.
Why Are Real-World Shipping Studies Inadequate?
Real-world shipping tests cannot ensure that companies are delivering safe and efficacious products to the patient for a few reasons: minimal control of hazards and inadequate representation of hazard exposures. Furthermore, attempting to demonstrate product robustness through real world shipping may even lead to a delay in regulatory approval. Let’s discuss a few of these problems in detail:
1. Minimal Control of Hazards: Companies who employ real-world shipping studies actively give up control of the shock, vibration, and low-pressure hazard exposures that the drug product will endure. In practice, you can only control the shipping lanes, thermal packaging systems, modes of transportation, and total duration (based on move-time and mileage).
- For example, a company may ship DP around the world with all applicable modes of transportation, thermal packaging systems that they intend to use commercially, and include an adequate number of miles (or total move-time) but this strategy lacks the ability to control distribution hazards except for temperature. There is no practical way to control the amount of shock or vibration exposures.
- In comparison, you have full control of each hazard when conducting a transport simulation.
2. Inadequate Shock Exposure: In real-world shipping studies where testing is conducted only at the pallet level (many times in an active unit), the shock exposures are significantly less severe than parcel shipping. With either pallet or parcel level shipping, biopharma companies can’t control the quantity of shock events or the intensity. Transport Simulation allows you the opportunity to control the number of shock events and the intensity (drop height) of shock events at both the parcel and pallet level, allowing you to evaluate drug product robustness against worst case shock exposures.
-
- You can’t ask your freight carrier to drop each pallet or parcel a specific number of times or from certain heights, so the best you can do it monitor for shock events. Furthermore, pharma companies typically use freight forwarder service levels that minimize shock exposures to ensure that each shipment is handled well and timely.
- With transport simulation you can easily include an appropriate number of shock events from the correct heights to ensure that you’re studying the effects of shock exposure to the DP appropriately.
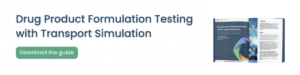
3. Inadequate Temperature Exposure: Shipping at the ideal temperature does not stress the drug product at the limits of the supply chain operating space. Most biologics are extremely sensitive to thermal challenges, and biopharma companies must evaluate appropriate temperature exposures, as temperature excursions will happen, and this should be conducted concurrently with physical distribution hazards for a realistic evaluation.
- Most companies conduct real-world shipping studies at the ideal shipping/storage temperature because that’s how they’ll be shipping their DP commercially. This strategy is inadequate because you should look to understand how the DP may be affected during temperature excursions in transit.
- With transport simulation you can easily include appropriate temperature exposures based on known product stability and capabilities of the supply chain. For refrigerated DP’s we recommend studying both high and low temperature exposures.
4. Lack of concurrent hazard testing: The inadequacy of temperature exposure also means that real-world shipping studies lack the concurrence of all transport hazard extremes. Because the shipments are conducted at optimum temperature, you can’t study the effect on DP from high temperature exposure concurrent with vibration, for example. This type of concurrent transport hazard extremes is easily included in a transport simulation study in the Modality Solutions Transport Simulation Lab.
5. Increased risk of import/export compliance: Many real-world shipping studies include international shipping lanes to get a long shipping duration or for global applicability of the study. However, this requires that you are compliant with all import/export regulations for multiple jurisdictions. Depending on where your DP is manufactured, packaged, and ultimately returned for analytical testing, a transport simulation study in our transport simulation lab in Indiana may not need to cross any (or not as many) international borders. This reduces your overall import/export compliance risk, especially for small-medium sized pharma companies. For larger biotech companies, no real-world shipping studies means that resources dedicated to import/export compliance are focused on actual shipments required for clinical/commercial needs.
6. Delays in Regulatory Approval: With real-world shipping studies instead of transport simulation, it’s difficult to stay on schedule. Biopharma companies could experience delays in their regulatory approval and commercial launch timeline because of an inadequate shipping validation strategy. In our experience, regulators are increasingly skeptical about real-world shipping validation – as they should be! Over the last 5-10 years, regulators have begun to question the adequacy of real-world shipping and accelerated package test standards for confirmation of DP robustness through distribution. Instead, they’re looking for well-designed, well-controlled, and realistic studies (like Transport Simulation).
7. More Expensive & Less Sustainable: Real-world shipping studies cost more money for biopharma companies to execute, and they are worse for the environment.
- Table 1 outlines a standard global distribution environment used for transport simulation and Table 2 provides a cost and environmental impact comparison. If conducting a single shipment of each lane in the real-world, freight and thermal packaging would cost about 13% more than a lab-based transport simulation. However, more international shipping lanes or triplicate testing for a real-world shipping study would extend/multiply the total cost. Due to the issues noted above for real-world shipping studies, most companies will conduct multiple international shipments to capture “enough” transport exposure to the DP, and this ultimately leads to a more expensive study with less robust exposures and less reliable data.
- In terms of sustainability and impact to the environment, real-world shipping studies with the same total move time as a transport simulation emits 17-18 times the amount of carbon, comparative toxic units (CTU) contributing to ecotoxicity, O3 contributing to smog, and SO2 contributing to acidification. These numbers clearly show how unnecessary extra real-world shipments have an impact on our environment and human health.
Table 1 – Global distribution network for shipping studies
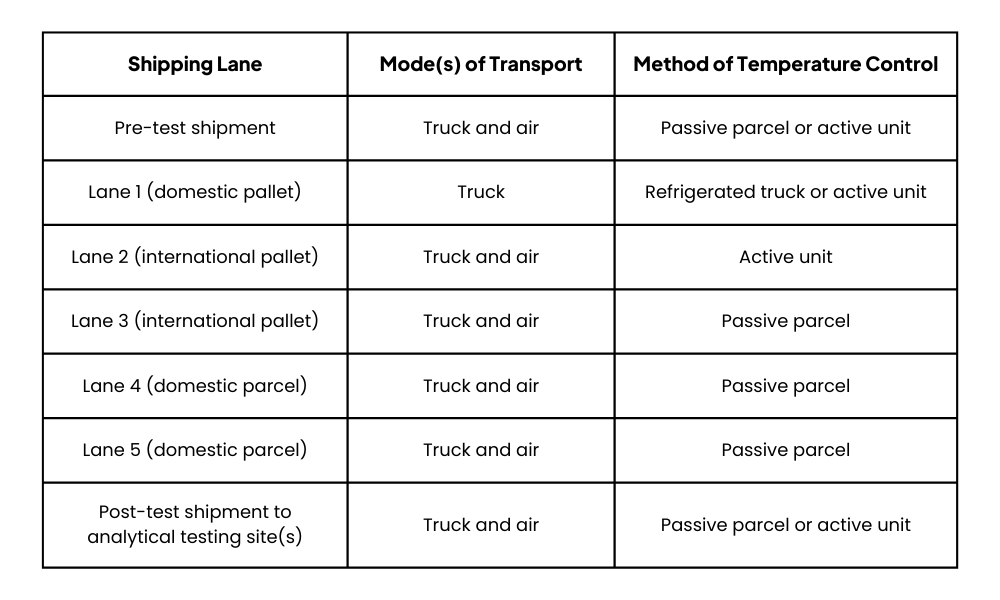
Table 2 – Cost & Environmental Impact Comparison
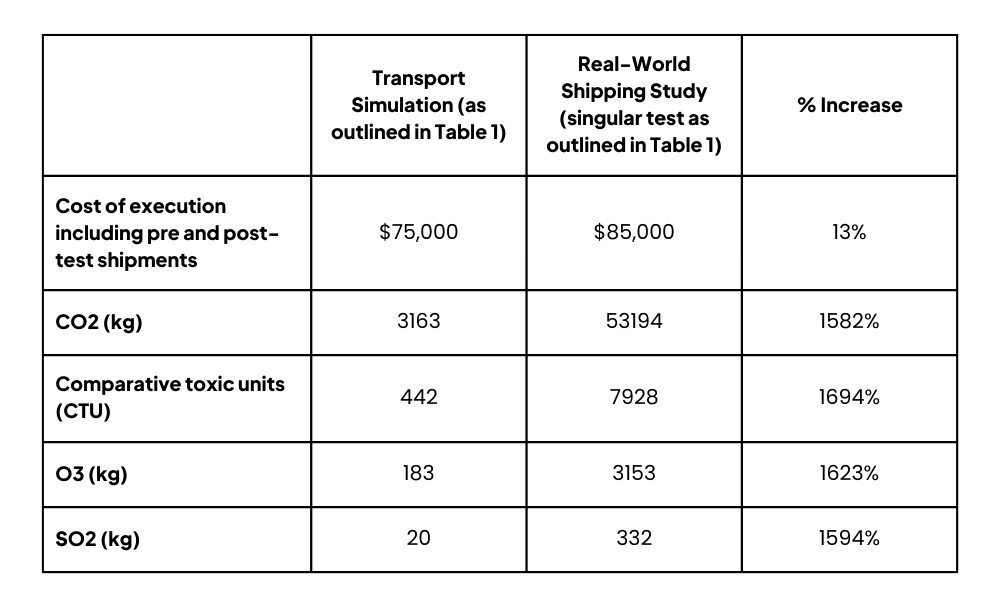
What is the appropriate alternative to Real-World Shipping Studies?
Ultimately, biopharma companies are unable to stress the drug product at the edges of the operating space for distribution, so they must turn to Transport Simulation to avoid wasted time, wasted resources, and inadequate data. With Transport Simulation comes full control of each hazard exposure, concurrent hazard testing, non-accelerated vibration profiles, and all relevant modes of transport. You can adjust transportation times to cover global distribution and potential future supply chain modifications, as well as realistic worst-case hazard levels (e.g., testing outside of 2-8 °C for a refrigerated drug product because temperature excursions will happen).
At Modality Solutions, we design each drug product transport simulation study custom to your product and known stability, your supply chain, expected hazards, and known capabilities. Every study is based on appropriate industry standards and the most up-to-date regulatory expectations. Our Advanced Transport Simulation Lab™ was specifically designed to study drug products with concurrent hazard testing.
Our team of cold chain engineers helps clients conduct risk assessments of the supply chain and distribution process, recommend mitigation strategies, validation master planning, design and execution of DP transport simulation studies, packaging robustness studies, thermal packaging selection and OQ evaluation/testing, PQ study design and reporting, regulatory filing support, assistance with regulatory responses, and more.
If you’re looking to explore better alternatives to real-world shipping studies, look no further than Modality Solutions and our Advanced Transport Simulation Lab™.