No Temperature Controls Necessary For Small Molecules? Are You Sure?
Ensuring Quality for Small Molecule Therapy Supply Chains in a Growing Market Managing the...
read Details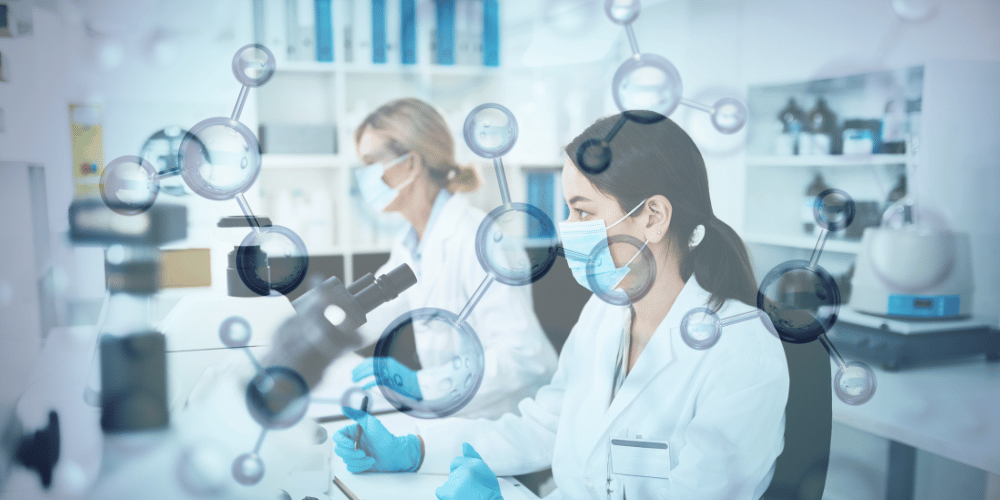
This six-part article series explores Cold Chain Process Validation, addressing the multifaceted challenges and evolving demands professionals like yourself face in ensuring product integrity from manufacturing to delivery. Amidst economic, technological, and regulatory pressures, the series begins with an overview of the cold chain validation process, emphasizing the need for comprehensive strategies to navigate competing priorities, sustainability initiatives, and the globalization of supply chains.
Click the links below to navigate to each article in the series:
Robust test standards and test methods must be in place in your quality management system. These test methods can be either a public standard (e.g. ASTM, ISTA, etc.) or be custom developed. Client-developed thermal profiles are a good example. Best practices require a data collection methodology, written protocols, and a summary of the data package. Any conclusions in a qualification report must be reviewed by your quality unit representative. Without these basics in place, your thermal profile may be questioned or rejected by the regulatory agencies. We recommend a focus on component qualification for passive thermal shipping systems and installation qualification for active refrigeration systems.
Component qualification focuses on gel ice performance, setting specifications, and critical-to-quality attributes for the passive shipper. Examples could include R-value, wall thickness, density, or even the weight of the packaging for simpler systems. Whatever attributes impact performance must be documented in user requirement specifications. These specifications should also include allowable tolerances and any substitute components that are available.
Installation qualification focuses on confirming manufacturer specifications were followed during the installation of the active refrigeration system. All operating parameters are maintained during load testing. Rather than focus on ‘thermal mapping’ inside an active refrigeration system, a dubious and flawed practice at best, we recommend your IQ focus on component specifications like BTU output, air flow/turnover, and R-value of the walls. This focus on specifications mirrors equipment installation qualification approaches followed in most manufacturing processes more closely than ‘thermal mapping’ of the inside of a trailer.
Both aspects, component qualification (CQ) and installation qualification (IQ), test critical operational controls, focusing on the key attributes of the type of system to be qualified. They also support robust performance during the system’s operational qualification (OQ).
Having test standards, thermal profiles, and verification shipments for transport lane qualification in place allows an organization to have confidence in the qualification of critical components and equipment, delivering products safely to patients. In other words, it provides for a robust CQ/ IQ test. The CQ/IQ ensures that the system and its components are installed correctly and adhere to the original manufacturer’s specifications.
The qualification deliverables of an organization’s product, primary containers, secondary packaging, insulated shippers, and drug delivery devices all require component specifications. The procedures for using and assembling them correctly must also be documented during CQ/ IQ. These CQ/IQ reports based on test data and procedures are the deliverables at this stage of transport process validation. They define the design space the systems are capable of operating in and the performance tolerances they can be expected to hold during operation qualification (OQ).
In the next article, you’ll learn about Operational qualification (OQ) and the critical role it plays in the transport validation process by testing critical parameters of the system/process at expected extremes while confirming that the process is adequate to deliver unadulterated products.
The pharmaceutical cold chain network is complex, but Modality Solutions makes it easy to simplify and streamline your cold chain. Working as a professional in the cold chain network means facing daily challenges. Just because the pharmaceutical cold chain network is complex doesn’t mean that your management system must be. Let our focused pharmaceutical cold chain engineering firm deliver results with our advanced technology and world-class engineers.
Here’s what you can expect:
Ensuring Quality for Small Molecule Therapy Supply Chains in a Growing Market Managing the...
read DetailsEnsuring the safe, effective delivery of small molecule drugs is more challenging than ever....
read DetailsAt a Glance: Cold Chain Engineering: Modality Solutions focuses on enhancing drug delivery through...
read Details