Building Resilience in Cell Therapy Supply Chains: Ensuring Timely and Safe Delivery
Executive Summary
In the fast-paced world of cell and gene therapies, building a resilient supply chain is crucial to ensure the timely and safe delivery of therapies to patients. This article explores the key principles and strategies involved in building and validating a resilient supply chain for cell therapies. Drawing insights from the presentation by Modality Solutions Engineering Manager, Robert Battista at the Allogeneic Cell Therapy Supply Chain Conference, we delve into the importance of supply chain resilience in ensuring timely delivery, operational flexibility, simplified scale-up, and compliance with safety and efficacy standards.
>> Download the Slide Deck that accompanies this blog.
Understanding Validation and Supply Chain Resilience:
To grasp the concept of building and validating a resilient supply chain, it is essential to define validation and supply chain validation.
- Validation refers to the confirmation that a specific process consistently produces the intended results.
- Supply Chain Validation demonstrates the consistent delivery of therapies to patients while maintaining safety, efficacy, and quality attributes. While temperature maintenance during shipping and storage is a crucial component, it is not the sole focus.
- Supply Chain Resilience, on the other hand, refers to the ability of a supply chain to prepare for and adapt to unexpected events, offering flexibility and operational agility.
The Importance of Supply Chain Resilience in Cell and Gene Therapies:
Building a resilient supply chain for cell and gene therapies holds several key benefits. Firstly, it ensures timely delivery to patients who are often critically ill and may have strict treatment timelines. Secondly, it provides flexibility to work with the best solution for each scenario, recognizing that every vial of therapy is crucial. Thirdly, a resilient supply chain simplifies the scale-up and expansion from clinical to commercial operations, enabling smooth transitions and accommodating increased shipments. Lastly, supply chain resilience plays a vital role in ensuring compliance and delivering safe and effective therapies to patients.
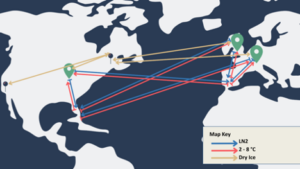
A recent example from a Modality Solutions client’s global commercial supply chain can be used to showcase the complexity of a global shipping strategy.
The green location markers you see in the image represent drug product manufacturing organizations situated in various regions. Building manufacturing options in multiple regions is crucial because it allows for closer access to patients. However, restricting each manufacturer to a specific region is not feasible due to cost, availability, and manufacturing slot constraints.
To begin, consider a single starting material collection organization located in Florida in the map above. This organization alone necessitates six shipping lanes. Three of these lanes involve refrigeration and are used for transporting materials to the manufacturing organization (indicated by the red lines). The other three lanes (indicated in blue), facilitate the transportation of the final drug product back to the clinic for administration.
In addition to the shipping lanes, it’s important to consider the precursors required for the manufacturing process, denoted by the blue location markers and gold lines in the image. These precursors often require completely unique supply chains and may even require different temperature conditions than the other shipping lanes we’ve established.
Therefore, with just two collection sites between the US and Europe, the number of shipping lanes increases to 16, and three distinct temperature presentations must be accounted for.
Let’s expand our perspective and envision the implications of having multiple collection organizations across the world. If you have approximately 30 collection sites in each region, the number of unique shipping lanes grows exponentially. The complexity of managing diverse shipping requirements, temperature conditions, and logistical challenges significantly increase as the number of collection sites multiplies.
The illustration above showcases the explicit need for resilient supply chains within drug product manufacturing organizations. A well-executed cold chain strategy ensures that companies have the flexibility to juggle numerous shipping lanes, temperature conditions, and precursor supply chains within one resilient cold chain strategy.
Principles of Building Resilience in Cell Therapy Supply Chain:
To achieve a resilient supply chain, two core principles can guide the process:
Multiple Shipping Solutions and Couriers:
Having multiple shipping solutions allows flexibility in choosing the best option for specific conditions and prevents potential delays caused by availability or accessibility concerns. Similarly, working with multiple couriers ensures alternative routes and mitigates issues related to specific hubs or delays.
Example: In the case of the global supply chain from the image above, here’s how Modality Solutions built supply chain resilience into our client’s cold chain strategy.
- Unique Shippers to Enhance Flexibility: The Modality Solutions team implemented four unique 2-8°C shippers for collected material. These shippers provided a large breadth of flexibility including different sizes which made different modes of transport more manageable. The shipper options also incorporated different pre-conditioning methods that to accommodate diverse global collection sites and their capabilities.
- Our team also recommended the implementation of two unique dry ice shippers for precursors and three unique LN2 shippers, both of which provided additional flexibility within the supply chain.
- Multiple Eligible Couriers: Our team also selected multiple eligible couriers for each shipping lane. The client had a single preferred courier that handled typical shipments, but additional, already-qualified couriers were waiting in the wings should the preferred courier experience any delays or problems.
However, a resilient supply chain must still ensure that the final therapy reaches patients with all safety and efficacy intact. Each shipping lane in the supply chain therefore requires a thorough qualification and validation processes. This step ensures compliance and the ability to manage multiple shipping solutions and couriers effectively. That’s where a Validation Master Plan comes in.
Robust Validation Master Plan:
A well-designed validation master plan provides a framework and guides the execution of validation activities. As cell therapy supply chains are increasingly complex, it’s important to avoid hyper-specific plans and focus on general guidelines (the “How To’s”) to allow for flexibility and adaptation to different shipping solutions, packaging configurations, and couriers.
Another important piece of ensuring flexibility is separating your pathways for demonstrating product quality assurance versus temperature control assurance during shipping. Each assurance should be separately demonstrated through:
- Product Quality Assurance: demonstrates that product quality is not adversely affected by worst-case distribution through:
- Exposure to worst-case supply chain hazards (shock, vibration, temperature, humidity, and/or pressure) under controlled laboratory conditions that are realistic and representative of your actual shipping conditions
- Followed by release studies to assess product quality
At the completion of this study, you have significant data that showcases a high confidence your product quality will not be adversely affected so long as the temperature is maintained during shipping. This allows your other supply chain studies to focus solely on temperature control.
- Thermal Control Assurance: demonstrates that storage and shipping temperatures will be maintained through:
- Operation Qualification (OQ) of equipment (shippers, freezers, etc.): OQs demonstrate that the equipment will meet baseline specifications under controlled conditions. OQs should cover all worst-case considerations.
- Many times, you can leverage studies performed by the vendor for an Operation Qualification. Most vendor qualifications are adequate, but it’s the product owner’s responsibility to confirm that the vendor testing meets the requirements of your specific use case.
- Performance Qualification (PQ) of shipping process (real-world shipments): PQs generate data on process performance for the qualified equipment interacting with human processes. PQs do not need to include worst-case conditions so long as they were adequately covered in your OQ.
Because of the complexity of the cell and gene supply chain, Modality Solutions strongly recommends a bracketing strategy to greatly reduce the number of shipments you might need.
Typical PQ Strategies Don’t Work for Cell and Gene Therapies
Traditional methods for Performance Qualification do not work for cell and gene therapies. The traditional approach of three PQ shipments per lane, per thermal shipping solution is too inefficient. If you think about solely the final product shipments with two collection sites, you’d be looking at 18 drug product shipments just to cover those two scenarios.
An efficient bracketing strategy can reduce the number of shipments required under PQ while still providing sufficient evidence that your shipping process operates in a state of control. Here’s how we recommend applying a bracketing strategy to your PQ:
- Comparable lanes can be studied together. If you have lanes where there will be a similar guided process and the expected severity of the lanes is comparable, you can bracket those together. This is especially applicable to patient/donor collection where you have a network of collection sites that will be following work instructions provided by your team in order to ship material.
- Shipper types can be bracketed. If the usage processes for the unique shippers are comparable, results can be leveraged across the different solutions (thermal shippers) within a supply chain.
- Special scrutiny should be paid to extra circumstances such as customs clearance. If you have specific lanes or couriers that will interact with international boundaries in different manners, pay attention to those circumstances.
The exact methods and amount of bracketing in your PQ strategy will be determined by your organization’s quality risk tolerance. As with all validation activities, all decisions should tie back to risk assessment and have adequate, documented justification.
Building and validating a resilient supply chain for cell and gene therapies is a critical aspect of ensuring timely and safe delivery to patients. By adopting multiple shipping solutions, working with multiple couriers, and implementing robust qualification and validation processes, companies can enhance their supply chain resilience. The focus should be on maintaining flexibility, simplifying scale-up, and ensuring compliance to provide patients with safe and effective therapies. With a resilient supply chain in place, the cell therapy industry can overcome unexpected challenges.
Contact Modality Solutions for more information