Pharmaceutical Cold Chain Is Complex
First published on April 9, 2015 on Cold Chain IQ – as a contributor, Hutchinson’s column, Global Cold Chain Connections, falls in the Supply Chain & Security category. It can also be viewed at http://www.coldchainiq.com/supply-chain-security/columns/today-s-pharmaceutical-cold-chain-network-is-incre/ Join Cold Chain IQ today to access informative cold chain articles.
By Gary Hutchinson
Competing priorities, changing expectations, cost pressures, sustainability initiatives, emerging markets — these are the challenges facing cold chain management professionals every day. Solutions that deliver value in the supply chain and enhance your regulatory reputation by ensuring compliance, product quality and safety are required every day, around the globe.
Today, engineers and manufacturers face economic and regulatory pressures, accelerating costs, technology changes, and the need to constantly adapt their business models. The advent of more widely distributed supply chains and many other influences demand greater investment in tools, expertise, and most importantly the human capital to succeed with some of the toughest challenges:
- Appropriate expertise and techniques to assess, control and communicate risk as part of an on-going management review process.
- A lifecycle approach to process validation including design, qualification, and verification.
- Better integration of product formulation, controlled environment logistics, and packaging design.
- Innovative, forward-looking quality controls, corrective and preventive actions (CAPAs) strategies, and root cause analyses for once straightforward processes that are highly complex today.
- The application of technology to achieve greater gains in all areas, including compliance, quality and safety.
Integrate your cold chain management systems.
The appropriate tools, expertise, and experience are critical when coordinating your activities to ensure safety, safeguard quality, maintain regulatory compliance, and prevent falsified, adulterated, and counterfeit product from entering the legal supply chain.
- Ensure compliance for high-value products in highly-regulated industries.
- Deliver packaging design and qualification.
- Conduct transport simulation testing with five environmental hazards – temperature, humidity, shock, vibration, and pressure.
- Develop transport validation strategies to support global regulatory requirements. Design controlled-environment logistics solutions that ensure product quality during transport.
Get results by focusing on implementation, not just on defining regulatory requirements. A properly integrated cold chain ensures regulatory compliance, product quality, and patient safety by providing a multi-layered approach that combines best practices of process validation, systems qualification and risk assessment with the most applicable monitoring and controls for qualified packaging.
What systems encompass an integrated cold chain management system?
A compliant cold chain management system is composed of a variety of components working in concert. An integrated cold chain management system ensures control of the distribution chain and consequently maintains the quality and the integrity of products. The seven components are: quality systems; risk management; product stability; qualification / validation; logistics management; partner management; and compliance management.
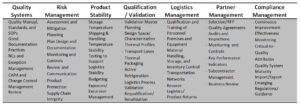
Systems – The First Pillar Developing mature quality systems is one of the biggest challenges and one of the most effective tools to manage a world-class cold chain logistics network. Making the systems work for you, and not the other way around, is the key to your success. Quality systems at their best establish, implement, and maintain a set of processes to provide the highest quality service to customers, highest level of effectiveness for management, and most robust compliance approach for regulators. At their worst, they just get in the way — adding only administrative burden and redundant reviews to an already complex and fast-moving network. I know. I have seen the value of an effective quality system that facilitates continual improvement, and I’ve seen the effects of a nominal one that provides only delays, derailments, and disasters!
An effective guide is needed to conduct a thorough review of your quality management system processes and tools to identify opportunities to provide structure and clarity to assist in the continual improvement of your controlled-environment logistics network. A review of the following elements of your quality systems should ensure these foundational capabilities are in place for your cold chain:
- Quality Manual, Standards, and SOPs – A review of your quality system structure focused on regulatory requirements, best practices, and ease of use. Match the size and complexity of the activities you are managing to the complexity of your documentation.
- Good Documentation Practices – Standardized templates, revision controls, and approval signatures are the cornerstones of an effective quality management system. Placing the appropriate practices in place for your technical documents, protocols, and reports are required for a successful audit.
- NCs and Exception Management – Non-conformances (NCs) and management of exceptions is an uncomfortable reality in a global controlled-environment logistics network. The proper documentation of non-conformances coupled with an effective way to manage and document the exception requires a well-defined and streamlined approach. Coupled with an effective management review, the handling of NCs is a key to continual improvement.
- CAPA and Change Control – Procedures for implementing corrective and preventative action (CAPA) help analyze processes, operations, records, complaints and other sources of data to confirm root cause and is one of the main roles of quality systems. A robust CAPA process uses appropriate statistical methods to identify trends and reoccurring non-conformances and provides investigational procedures. Controlling change in your organization and identifying a planned approach to CAPA resolution, including effectiveness verification, is necessary to drive continuous improvement.
- Management Review – Quality systems need management support to enact change. A management review process requires the identification of key performance indicators with process control limits in place to determine when action is required. Along with self-assessments and audits, guideposts for the executive team to understand quality failures, process needs and updates on improvements is an essential feedback loop needed to build into your quality system.
Use these tools to assess your capabilities, create time-bound improvement plans, and mentor your team on the opportunities for improved profitability and efficiency. Conducting a quality systems maturity assessment can lead the way to breakthrough performance.